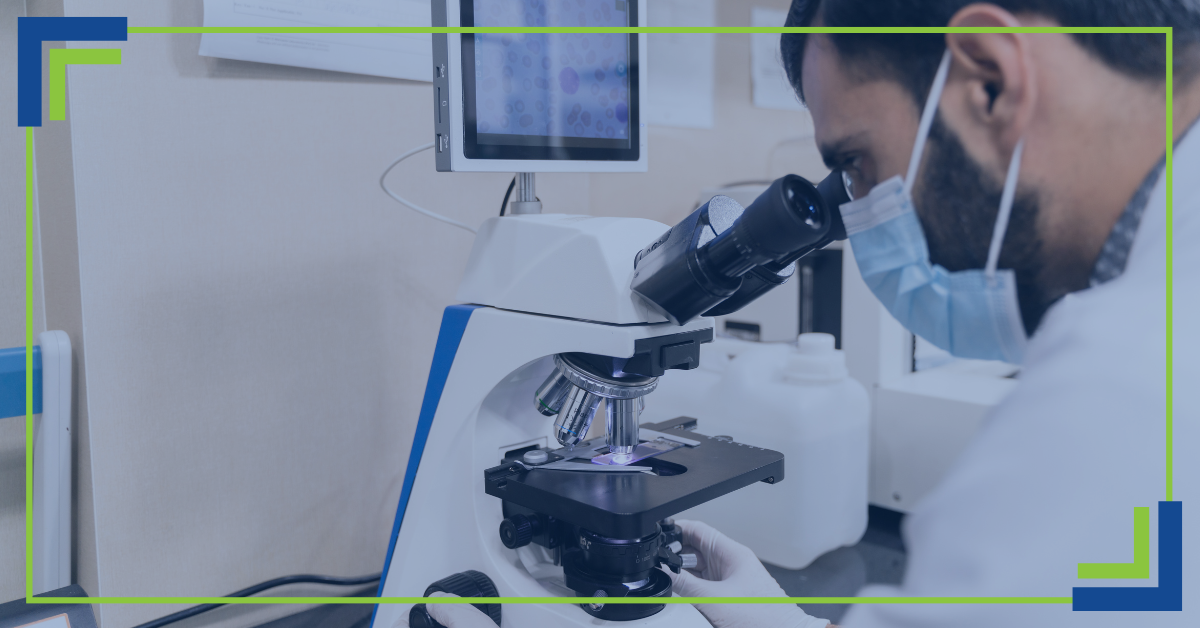
When performing scientific research, different types of laboratory equipment are needed to conduct experiments and analyze information correctly. They help you collect data, measure substances, and observe changes in a controlled environment.
One tool that we are all likely familiar with is the microscope. Many scientific fields require the ability to see tiny details that aren’t visible to the naked eye. Another tool, a balance, helps to measure the exact mass of a substance. Along with other pieces of common lab equipment, these tools make it possible for scientists to standardize procedures with consistent experimental methods. This allows them to conduct experiments with the confidence that other researchers will follow the same procedures and achieve the same outcomes. By using the same tools and techniques, scientists can compare their findings with others and build upon existing knowledge in the field. This consistency in scientific methods also reduces the margin of error and increases the reliability of the research outcomes.
But what would happen in the same kind of lab if it didn’t have any of the common lab equipment needed for conducting experiments? Well, if there weren’t any microscopes, scientists wouldn’t be able to observe tiny microorganisms, limiting their ability to study cells or bacteria. Also, without the proper tools like balances or pH meters, researchers may not be able to accurately measure substances, affecting the validity of their findings. A lack of proper laboratory equipment could also compromise a lab’s safety, increasing the risk of accidents. Without the proper tools to get the job done, the scene in the lab would become chaotic, progress couldn’t continue, and few to no discoveries would be made.
Basic Laboratory Equipment
Every lab should at least have these pieces of laboratory equipment:
- Microscopes to allow the examination of tiny cells and molecules
- Centrifuges that spin samples to separate components
- PH meters to measure how acidic or basic a solution is
- Balances to give you an ingredient’s exact mass or to compare the masses of two ingredients
- Incubators for keeping bacteria and cells at optimal and consistent temperatures
Scientists need the items on this lab equipment list in order to perform research and continue discovering new things about our world. At BaneBio, we’re here to help you set up or upgrade your lab.
Advanced Equipment for Specialized Research
Now, let’s talk about some advanced scientific tools that are needed for research:
- Spectrophotometers measure light absorption and transmission for analyzing chemical composition.
- NMR spectrometers look at the core of atoms, studying atomic nuclei’s magnetic properties to show molecular structures and interactions.
- Mass spectrometers are used when analyzing the mass characteristics of ions to provide information about the composition and structure of compounds.
- Chromatography systems separate the molecules within complex mixtures, like the sorting hat in Harry Potter.
- Polymerase Chain Reaction (PCR) machines act as copy machines for DNA, creating millions of copies in a matter of seconds.
At BaneBio we have the advanced tools that are essential for your high-level scientific research.
Safety Equipment
In the lab, it’s important to have a safety-first policy. Every lab should have fume hoods designed to protect people from toxic fumes. Safety goggles are needed to shield your eyes from chemicals that may splash or be spilled. Emergency showers and eyewash stations can provide quick decontamination. Meanwhile, personal protective equipment (PPE) like gloves and masks provide a barrier to protect you from harmful substances. Of course, a lab also needs fire extinguishers in case there’s a mishap with a Bunsen burner.
Automation and Robotics
Now, it’s time to think about technology. Liquid handling robots, high-throughput screening systems, and automated sample preparation systems are changing how experiments are done. Liquid handling robots take the repetitive pipetting tasks off your hands. Automation including high-throughput screening systems speed up the discovery of new drugs by screening thousands of compounds at the same time. By assigning mundane tasks to these automated systems, scientists can free up their valuable time for more engaging and intellectually stimulating tasks.
Maintenance and Calibration
Last but not least, maintenance and calibration both matter. Regular maintenance tasks, like cleaning and calibrating lab equipment help instruments stay in good shape. So, don’t skip simple maintenance tasks.
In a science lab, calibration tools can vary depending on the instruments being used. Some of our commonly used calibration tools include:
- Calibration weights for balances and scales
- pH buffers for pH meters
- Thermometers for temperature calibration
- Multifunction calibrators for electronic instruments
- Pressure gauges for pressure calibration
- Tachometers for speed calibration
It’s important to establish regular calibration schedules for your laboratory equipment’s accuracy. This helps to maintain the reliability and precision of scientific instruments. By performing regular calibration you can be certain that the measurements you take are consistently accurate, and you can have confidence in the data your equipment gives you.
Invest in Discovery
You need to have the right laboratory equipment for scientific progress. Whether it’s basic tools like microscopes and centrifuges or more advanced gear like spectrophotometers and Polymerase Chain Reaction (PCR) machines, each piece is important for learning more and making advanced scientific discoveries. So, be sure you invest in updated equipment, prioritize safety, and welcome scientific innovation. When you work with BaneBio you’ll have the equipment and materials you need for experiments and scientific discoveries. Reach out to us for all of your laboratory needs.