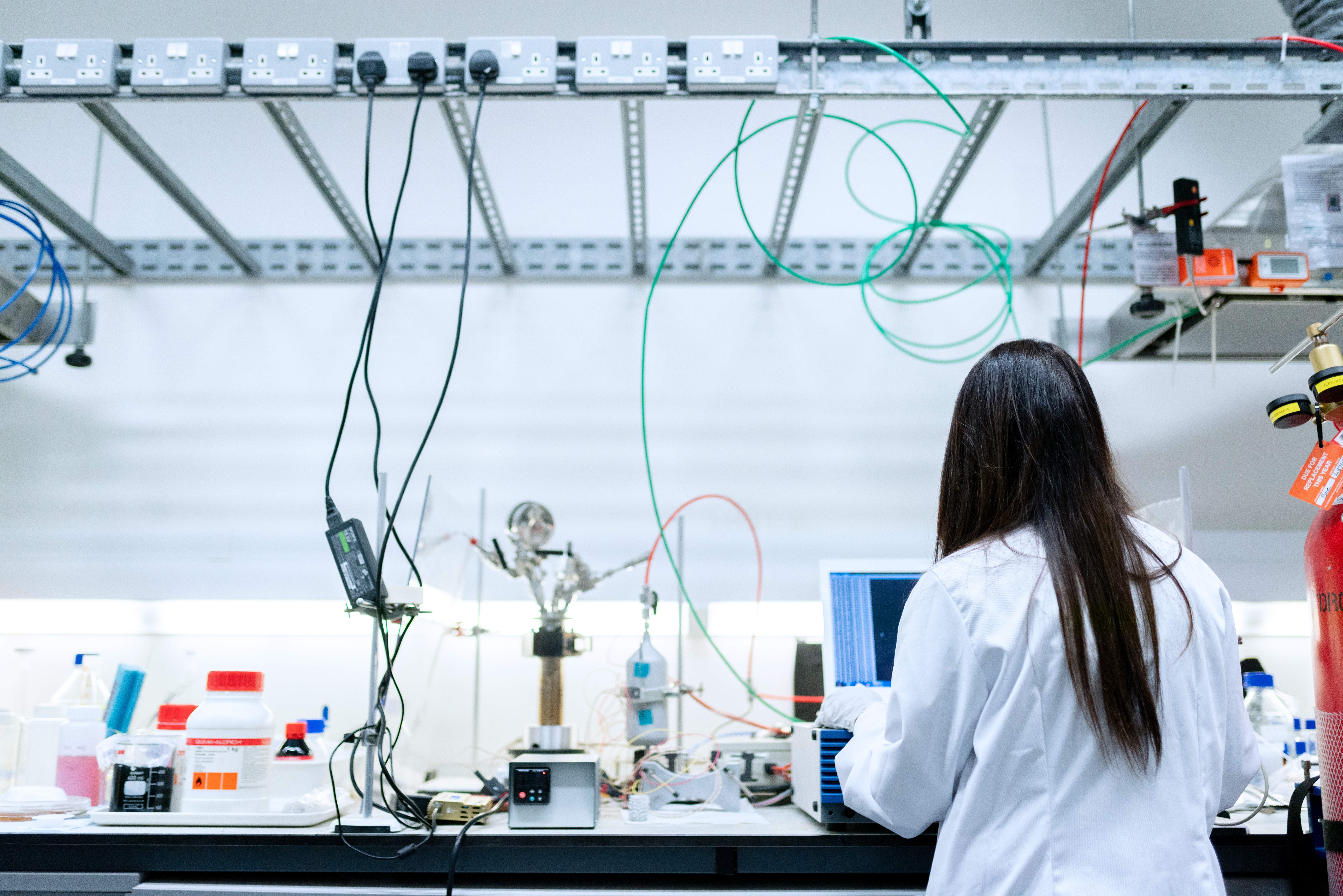
Your cold storage units are the unsung heroes in your lab. They’re the pieces of equipment you never think about until they stop working.
Here are five best practices for your cold storage units:
1. Make Sure The Cold Storage Unit is Evenly Stocked
An improperly stocked freezer is prone to extreme temperature shifts when the doors are opened. A good rule of thumb is to try to keep the equipment at least 30% full if possible. If this isn’t possible, add a few gel packs or sealed water bottles to keep the temperatures consistent.
Conversely, don’t overstock your cold storage. Not only will this block airflow inside the unit, it will cause your staff to keep the doors open longer searching for items.
Avoid stocking materials that are extremely sensitive to temperature fluctuations on the top or bottom shelf of the unit. Instead, place them on the middle shelves of the unit to help them maintain a steady temperature.
2. Keep Your Cold Storage Equipment Cleaned and Sanitized
The best way to discourage bacterial contamination in your cold storage units is to make sure they are regularly cleaned and disinfected. A soft rag and a neutral cleaner is best for this task.
If possible, remove shelves and wipe them down, allowing them to dry completely before returning them to the unit. Clean both the interior and the exterior of the unit, paying attention to the coils as well.
To properly clean the condenser coils, use a vacuum, air jet, or a dry brush. Clean coils keep the heat exchanger working optimally, increasing the lifespan of the equipment while reducing its energy usage.
Never use bleach or harsh disinfectants that could potentially harm your equipment.
3. Frost Control
While no laboratory wants to place a cold storage unit out of service, it’s necessary to schedule a defrost at least once per year, or whenever the frost is more than one centimeter thick. This increases the unit’s energy efficiency and ensures an even temperature. Use this time to check all gaskets and door seals to make sure they’re still sealing properly.
4. Labels Facing Out
Position all items in cold storage with the labels facing out to ensure staff can quickly find what they’re looking for. This helps reduce the amount of time the unit’s doors are open. Discourage random repositioning of stored items. Your lab may even benefit from a spreadsheet that outlines where items are stored in the unit.
5. Replace Cold Storage Units In Time
As cold storage units age, they’ll become increasingly unreliable and consume more energy. You may find your lab is frequently repairing older units. As a rule, the average lifespan of a cold storage unit is twelve to fifteen years. If your equipment is nearing its end of life, consider purchasing a new one or replacing it with a newer used one.
BaneBio is Your Partner for New and Used Cold Storage Equipment
If it’s time to replace your lab freezer or refrigerator, BaneBio has the products you need. Whether you’re looking at a new piece or a certified used piece, browse our products and find your perfect replacement. We accept trade-ins and purchase used lab equipment as well. Reach out to us and learn more!